Audi Repair Shop Doylestown
Call 267 279 9477 to schedule a appointment
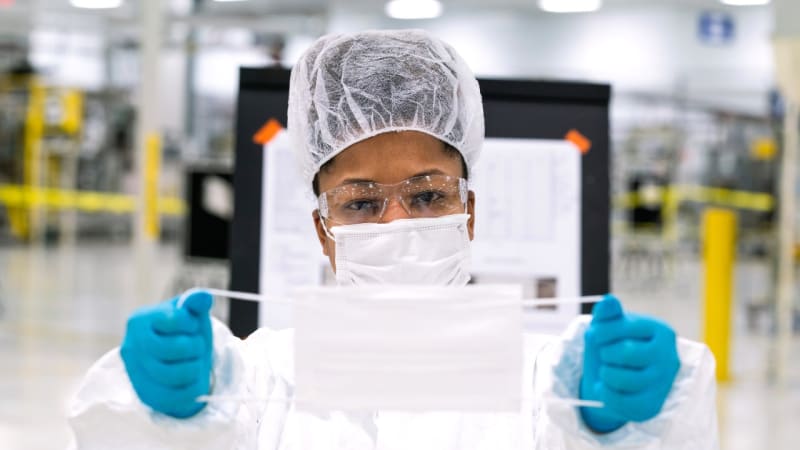
Ford on Monday offered some new details on its expanding push to produce badly needed medical equipment to fight the coronavirus, saying it’s now producing face masks at a Detroit-area transmission plant, making reusable medical gowns out of airbag material and helping a medical supplier ramp up production of COVID-19 field testing kits.
In addition, Ford said it will kick off production Tuesday of a powered air-purifying respirator it designed with consultation from 3M. Production will take place at its Vreeland facility near its Flat Rock Assembly plant, where it builds the Mustang and Lincoln Continental, using about 90 paid UAW volunteers, with enough capacity to manufacture 100,000 units, but no timeline offered.
Ford last month announced it was partnering with 3M to increase production of the company’s powered air-purifying respirators, and working on a new design for a waist-mounted, battery-powered blower that sends filtered air into a hood with a plastic shield for respiratory protection. The design uses off-the-shelf parts like an F-150 seat blower fan and paint-shop hoods, a portable battery and 3M high-efficiency air filters. Ford said it developed the unit, which provides a supply of filtered air for up to eight hours, in less than four weeks.
Ford said it has been working closely with the CDC’s National Institute for Occupational Safety and Health and expects to have provisional approval for the device by the end of the month. Once in production, 3M will distribute the respirators directly to health care providers through its distribution network. Officials from both companies said they are working outside of the Defense Production Act, which President Trump invoked for General Motors in its push to manufacture ventilators, but in close coordination with the CDC and FEMA.
Any profits received from the respirator units will be donated to COVID-19-related nonprofits, the companies said.
Ford said it has joined with supplier Joyson Safety Systems and consulted with a Detroit-area health system to design a reusable, washable medical gown using nylon material normally used to make airbags for Ford vehicles. Production will reach 75,000 gowns per week by Sunday and scale up to 100,000 gowns per week for the week of April 19 and beyond. Joyson is handling the cutting and sewing of 1.3 million gowns by July 4.
The company is also helping Thermo Fisher Scientific triple its production of COVID-19 test kits with help from engineers from its nearby Kansas City Assembly Plant, including by converting machinery that ran glass vials for other products to run the plastic vials necessary for drive-through coronavirus test collection.
Ford is also now manufacturing face masks for use by its own employees at its Van Dyke Transmission Plant in suburban Detroit using around 30 paid UAW volunteer workers in a cleanroom setting, with plans to increase staffing to 80. The company is also pursuing certification for medical use as well. It also said it had produced more than 3 million plastic face shields for medical personnel and first responders as of April 13, with plans to begin manufacturing ventilators at its Rawsonville Components Plant next week.
Relate Video:
from Autoblog https://ift.tt/2wADlEO